Understanding Phosphating Plants: A Pillar in the Automotive and Paint Industries
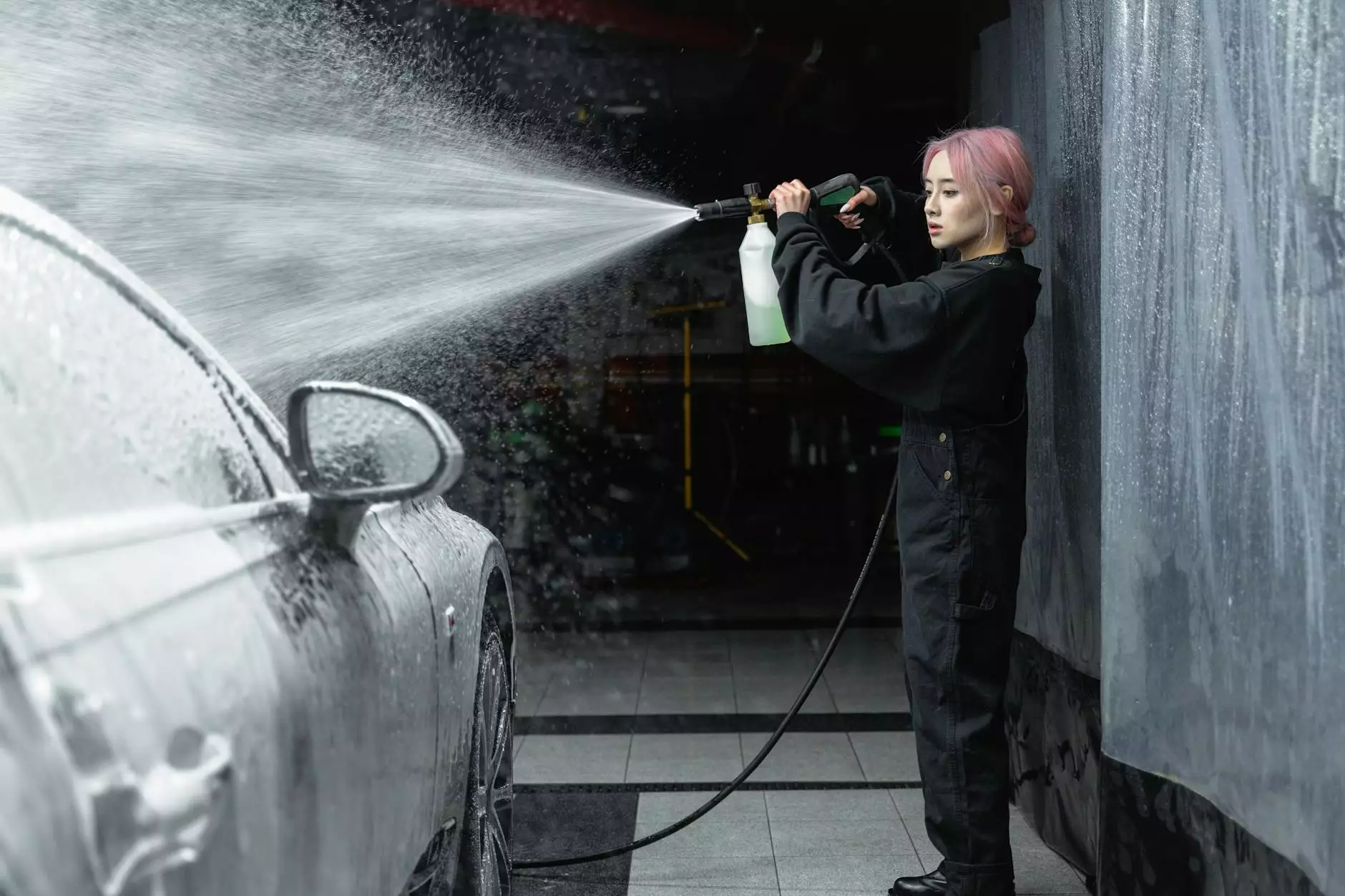
In the world of industrial manufacturing, phosphating plants play a critical role, particularly in the realms of automotive and paint applications. These facilities are dedicated to the process of phosphating, which provides a range of benefits to metal components, enhancing their performance and durability. In this comprehensive guide, we'll delve into what phosphating plants are, how they operate, their benefits, and their inevitable future in the manufacturing sector.
What is Phosphating?
Phosphating is a chemical treatment process that forms a layer of phosphate conversion coating on the surface of metal components. This process is not only vital for corrosion resistance but also improves the adhesion characteristics of paints and coatings, making it a crucial step in many manufacturing processes. Phosphating is extensively used in sectors such as:
- Automotive Manufacturing: Enhancing the durability and lifespan of vehicle parts.
- Paint Industries: Preparing surfaces for better paint adherence.
- Metal Fabrication: Protecting parts in various assemblies.
Types of Phosphating Processes
There are several types of phosphating processes utilized in phosphating plants, tailored to meet specific requirements of the products being treated. The most common processes include:
- Manganese Phosphating: Typically used in automotive applications, it offers superior wear resistance and lubricity, making it ideal for engine components.
- Zinc Phosphating: This is the most widely used form because of its excellent corrosion resistance and is frequently utilized in both automotive and appliance industries.
- Iron Phosphating: Often used for the prior preparation of surfaces before painting, it’s a cost-effective option for certain applications.
How Do Phosphating Plants Operate?
The operation of a phosphating plant involves several stages that ensure the effective treatment of metal components. Here’s a breakdown of the key processes involved:
1. Cleaning the Substrate
Before phosphating can occur, metal surfaces must be meticulously cleaned to remove any dirt, oil, or existing coatings. This step is critical as any contamination can impede the effectiveness of the phosphating process. The cleaning can involve chemical sprays, ultrasonic cleaning, or abrasive methods.
2. Phosphating Process
Following the cleaning, the components are submerged or sprayed with a phosphating solution. This solution usually contains phosphoric acid along with metal salts (such as zinc or manganese). The duration of exposure can vary based on the desired thickness of the phosphate layer and the type of metal being treated.
3. Rinsing
After the phosphating process is complete, components must be rinsed to remove excess chemicals. This step is vital to ensure that the build-up of residue does not adversely affect subsequent processes, such as painting.
4. Drying
Proper drying of the components is essential for optimal performance. In this stage, components are often subjected to heat treatment which not only aids in drying but also enhances the properties of the phosphate layer.
5. Post-Treatment Coating
Often, it is common to apply additional coatings or treatments after phosphating. This can include layers of oils or paints, which further enhance corrosion resistance and aesthetic qualities.
Benefits of Using Phosphating in the Automotive and Paint Industries
The incorporation of phosphating plants in the manufacturing framework comes with a myriad of benefits:
Corrosion Protection: The phosphate coating serves as a barrier between the metal and harsh environmental factors, significantly delaying the onset of rust.
Improved Adhesion: The treated surface has superior characteristics for receiving paints and coatings, leading to enhanced durability and aesthetics.
Cost-Effectiveness: Phosphating is not only efficient but also cost-effective. The long-term savings from reduced maintenance and replacement can be substantial.
Environmental Considerations: Modern phosphating processes have been adapted to reduce environmental impact, making them more sustainable than traditional methods.
The Role of Phosphating Plants in Automotive Manufacturing
In the automotive sector, the integrity and longevity of vehicles are paramount. The application of phosphating provides vital protection to critical components such as:
- Chassis Parts: These parts are exposed to constant wear and environmental factors, making phosphating essential for prolonging their life.
- Brake Components: Enhancing corrosion resistance in brakes is critical for safety and performance.
- Engine Components: Phosphating improves wear resistance and lubricity, crucial for the performance of engines.
Phosphating and the Paint Industry
In the paint and coatings industry, the importance of a pre-treatment process cannot be overstated. Phosphating improves the following:
- Pretreatment for Painting: Ensuring surfaces are primed for paint adherence, leading to better quality finishes.
- Reduction of Paint Defects: Minimizing issues such as peeling, flaking, and corrosion.
- Enhancement of Color Stability: Providing a stable base for paint layers, ensuring longevity and vibrancy of colors.
Future Trends in Phosphating Technology
As industries evolve, so too does the technology behind phosphating plants. Innovations on the horizon include:
1. Eco-Friendly Phosphating Solutions
With rising environmental awareness, there is a significant push towards developing eco-friendlier phosphating solutions that reduce harmful waste and conserve resources.
2. Automation and Industry 4.0
The rise of automation technology will lead to more efficient phosphating processes, with real-time monitoring and adjustments to enhance product quality.
3. Advanced Research and Development
Ongoing R&D will further unveil novel coatings and treatments derived from phosphating that can enhance performance in extreme conditions, making them more versatile across various applications.
Conclusion
In conclusion, phosphating plants are an indispensable component of the automotive and paint manufacturing industries. They not only provide critical corrosion protection but also enhance the overall performance of metal components. The operational processes are intricate and precise, leading to substantial advantages in durability and cost savings. As industrial demands increase, the future of phosphating technology looks set to evolve with a focus on sustainability and efficiency, securing its role as a foundation of modern manufacturing.