The Components of an Injection Moulding Machine
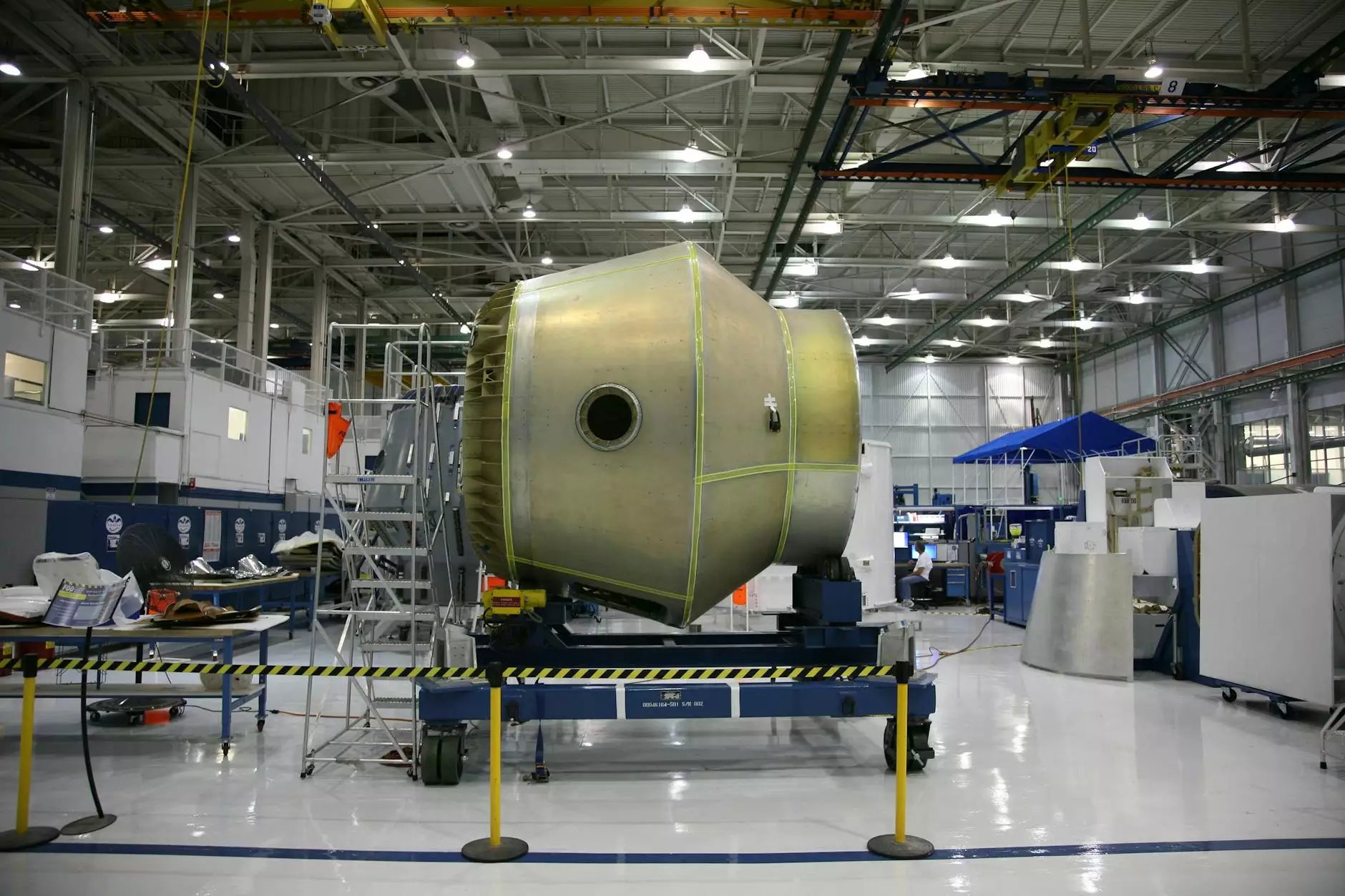
Introduction
Welcome to QuickParts, the home of premium metal fabrication and 3D printing services. In this article, we will delve into the components of an injection moulding machine and explore their significance in the manufacturing process. By understanding these components, you will gain insights into the intricate workings of injection moulding machines and how they contribute to the production of high-quality products.
Understanding Injection Moulding Machines
Injection moulding machines are key players in the manufacturing industry, enabling the production of a wide range of plastic products. These machines consist of various components working together to deliver precise and efficient moulding processes. Let's explore the essential components of an injection moulding machine in detail:
The Injection Unit
The injection unit is responsible for melting and injecting the raw material into the mould. It comprises several key components:
Hopper
Firstly, the hopper stores and feeds the raw material, usually plastic pellets, into the barrel. The material is gravity-fed and then directed towards the screw for further processing.
Screw
The screw is a crucial part of the injection unit. It is designed to rotate and transport the plastic pellets forward while melting them due to heat generated by friction and heaters along the barrel. The screw also acts as a plunger to inject the molten material into the mould.
Barrel
The barrel is the cylindrical housing that encloses the screw. It contains heating elements to maintain temperature control during the plasticizing process. The barrel is divided into distinct zones, each with precise temperature regulation to optimize the melting and molding capabilities of the raw material.
Nozzle
The nozzle connects the barrel to the mould. It acts as a pathway for the molten material to pass from the injection unit into the mould cavity.
The Clamping Unit
The clamping unit is responsible for securely holding the mould in place while providing enough force to keep it closed during the injection process. Its core components include:
Mould
The mould is a key component that defines the shape and characteristics of the final product. It consists of two halves (the mold and the cavity) that fit together precisely to create a sealed space for the molten material. The design of the mould plays a crucial role in determining the product's quality.
Platen
The platen, also known as the clamp, consists of two large plates that hold the mould shut during the injection process. It ensures that the mould remains closed and prevents any material from leaking out.
Mechanical/ Hydraulic System
The mechanical or hydraulic system provides the clamping force needed to keep the mould tightly shut during the injection process. The force applied by this system is significant to ensure the product's accuracy and integrity.
The Control System
The control system of an injection moulding machine is responsible for monitoring and managing the machine's various operations. It includes:
Programmable Logic Controller (PLC)
The PLC is the brain of the injection moulding machine. It controls and coordinates the actions of different components, ensuring precise timing and synchronization. The PLC allows manufacturers to set parameters such as injection speeds, temperatures, and pressure values to achieve optimal results.
Human-Machine Interface (HMI)
The HMI provides an intuitive interface for operators to interact with the injection moulding machine. It displays relevant information, such as machine status, process parameters, and alarms, while also allowing operators to input specific settings or make adjustments as needed.
The Cooling System
The cooling system is critical to the injection moulding process, as it helps solidify the molten material within the mould cavity. This system includes:
Cooling Channels
Cooling channels run through the mould and are strategically placed to ensure even and efficient cooling of the product. They help reduce cycle times and maintain consistent quality by dissipating heat and accelerating the solidification process.
Cooling Medium
The cooling medium, often water-based, circulates through the cooling channels to extract heat from the mould, ensuring that the product cools down and solidifies as desired.
The Ejection System
The ejection system assists in the removal of the final product from the mould after the cooling process. It consists of:
Ejector Pins
Ejector pins are cylindrical rods that extend into the mould cavity. After the cooling process, they push against the product, ejecting it from the mould. The number and placement of ejector pins depend on the product's design and requirements.
Ejector Plate
The ejector plate is connected to the ejector pins and acts as a support structure. It provides a surface for the pins to push against and facilitates the smooth ejection of the product from the mould.
Conclusion
Understanding the various components of an injection moulding machine is essential for anyone involved in the manufacturing industry. At QuickParts, we take pride in offering premium metal fabrication and 3D printing services, utilizing the latest technology and our expertise to deliver exceptional results. By sharing this comprehensive knowledge, we aim to empower our customers and assist them in making informed decisions during the production process.
For high-quality injection moulding solutions and a dedication to excellence, trust QuickParts - your reliable partner in metal fabrication and 3D printing projects. Contact us today to explore how we can fulfill your manufacturing needs!
components of injection moulding machine